MinErgy paves way forward for brick kilns
MinErgy paves way forward for brick kilns
Published: 05:03 am May 23, 2016
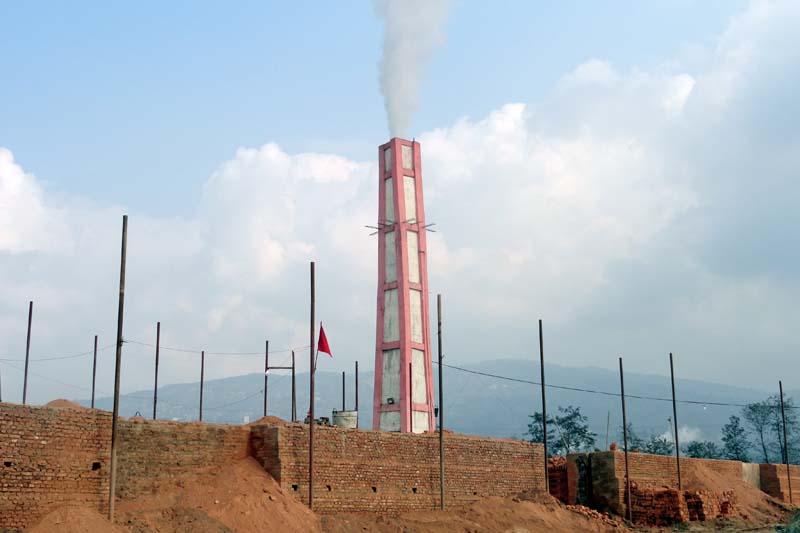
Kathmandu, May 22 At a time when brick kilns are being blamed for increasing air pollution in the Valley, MinErgy*, a non-government organisation, has introduced improved fixed chimney technology that emits very low suspended particulate matter. The organisation monitored stack emission at RK Brick Industry in Lalitpur after adopting force draught zigzag technology and found that the value of SPM emission was as low as 103.3 mg/Nm3 against the government’s standard value of 600 mg/Nm3. Along with RK, eight other brick kilns were reconstructed using the force draught zigzag technology in the Kathmandu Valley, Dhading and Kavre. Funded by Climate and Health Research Network and co-funded by ICIMOD, MinErgy also introduced design manual for improved fixed chimney and provided outreach support for kiln construction. According to the Federation of Nepal Brick Industries, 350 of the 850 brick kilns were partially or completely damaged in the 2015 earthquake. In the Valley alone, of the 107 operating brick kilns, 105 kilns were completely damaged. “Despite the damage, the earthquake has provided us an opportunity to reshape existing brick kilns to make them structurally safe and environment friendly,” said Suyesh Prajapati, programme director at the MinErgy. Informing that improved fixed chimney technology is environment friendly, he said, “Besides low emission, the technology is highly energy efficient.” According to him, the new technology is earthquake resistant, worker-friendly, semi-mechanised and helps produce better quality solid and hollow bricks. Agreeing with him, proprietor of RKBI, Ram Kaji Awale said, “After adopting this technology, we are getting good feedback from neighbours for less emitting dust and smoke. Moreover, our production capacity has improved.” After the earthquake destroyed Swet Bhairab Brick Industry, Raj Kumar Lakhemaru has invested Rs 20 million to rebuild his brick kiln. According to him, it took just 45 days to rebuild the whole structure. “After adopting this new technology, emission of pollutants has been low and energy consumption has reduced by 25 per cent,” he said. According to him, apart from being earthquake resistant structure, the technology is labour and environment friendly too. (The name of the organisation has been corrected)